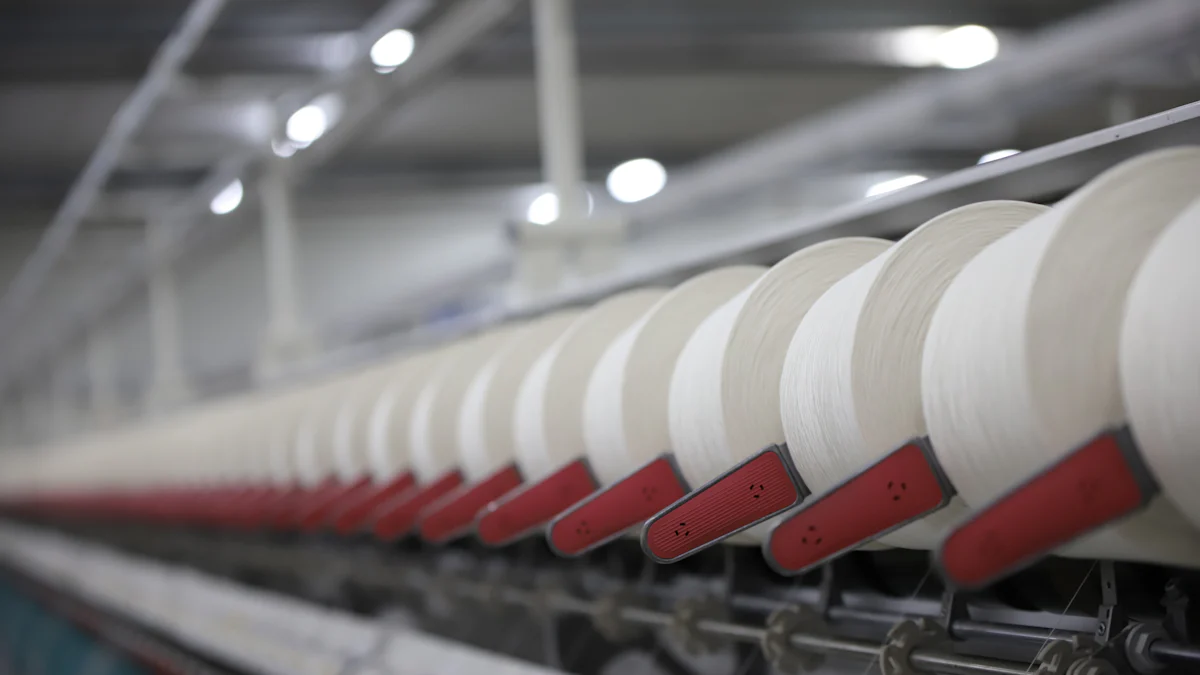
Static electricity often disrupts textile production. It causes fibers to stick together, slows down machines, and creates safety hazards. You can solve these problems with anti-static agents. These agents reduce static buildup, ensuring smoother operations. By 2025, advancements in these solutions will make textile processing more efficient and reliable.
Understanding Static Electricity in Textiles
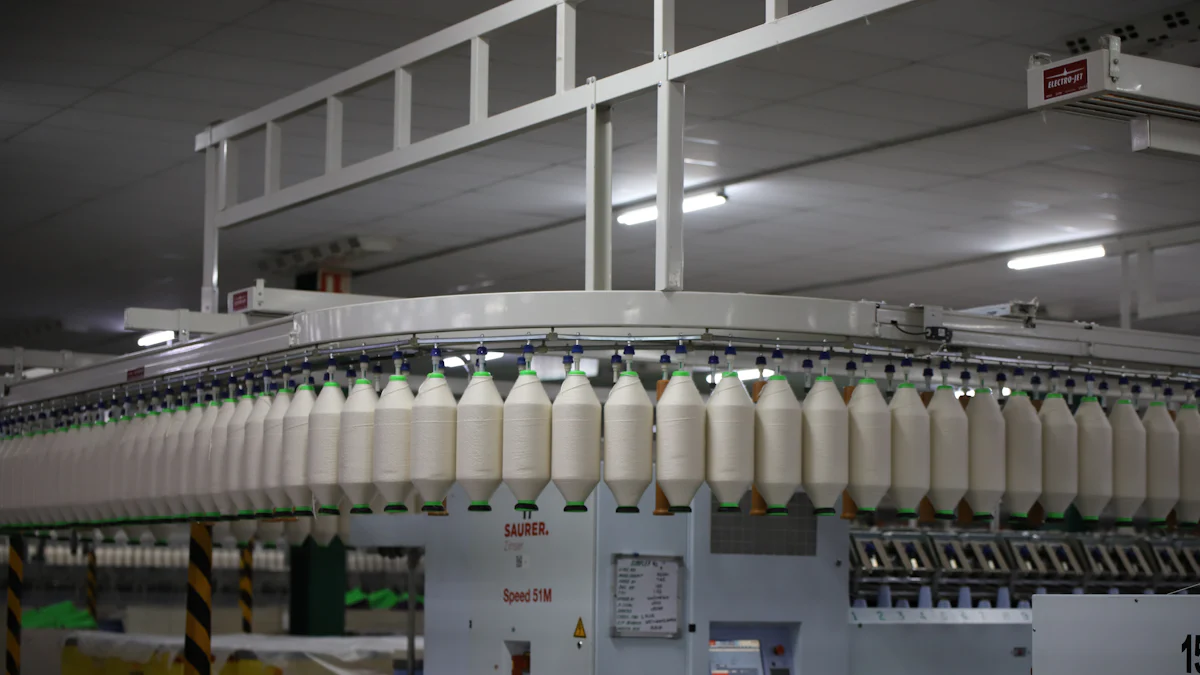
Causes of Static Electricity in Textile Processing
Static electricity forms when two surfaces rub against each other and exchange electrons. In textile processing, this happens frequently as fibers move through machines or come into contact with one another. Synthetic materials like polyester and nylon are especially prone to static buildup because they do not conduct electricity well. Dry environments also make the problem worse since moisture usually helps dissipate static charges. You may notice static electricity more during colder months when humidity levels drop.
Impact of Static Buildup on Textile Manufacturing
Static buildup can disrupt your production process in several ways. Fibers may cling together, making it harder to separate and process them. This can slow down machines and reduce efficiency. Static electricity can also attract dust and dirt, which lowers the quality of your final product. In some cases, sparks caused by static discharge may even pose safety risks, especially in environments with flammable materials. These issues can lead to higher costs and delays if not addressed properly.
Why Static Control is Essential for Modern Textiles
Controlling static electricity is crucial for smooth and efficient textile production. By managing static, you can prevent machine slowdowns and improve the quality of your fabrics. Anti-Static Agents play a key role in this process. They help reduce static buildup, ensuring that fibers move freely and machines operate without interruptions. In today’s competitive market, maintaining high-quality standards and efficient production processes is essential for success. Static control helps you achieve both.
How Anti-Static Agents Solve Static Issues
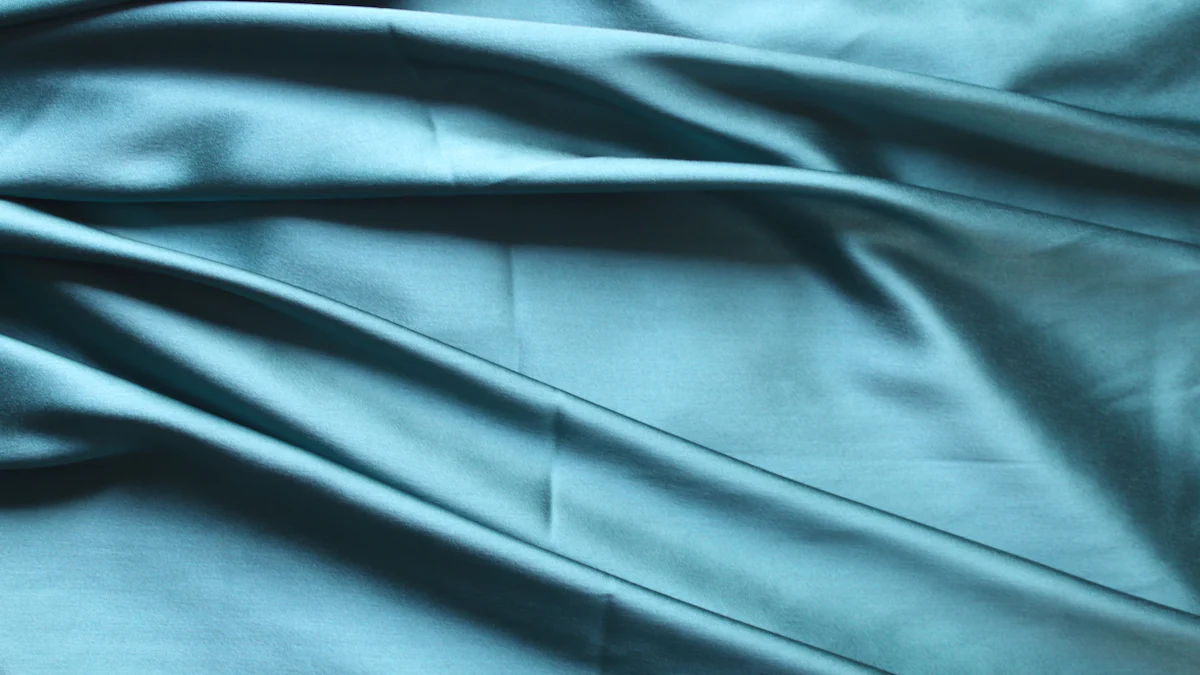
Mechanism of Action: How Anti-Static Agents Work
Anti-static agents work by reducing the buildup of static electricity on textile surfaces. They achieve this by increasing the conductivity of fibers, allowing static charges to dissipate quickly. These agents often contain compounds that attract moisture from the air. The added moisture helps neutralize static charges, especially in dry environments. Some anti-static agents also form a thin, invisible layer on the fabric. This layer prevents friction between fibers, which is a major cause of static electricity. By using these agents, you can ensure smoother processing and fewer disruptions during textile manufacturing.
Types of Anti-Static Agents for Textile Applications
You can choose from several types of anti-static agents depending on your needs. Surface-active agents, such as cationic and nonionic surfactants, are common. These agents reduce static by altering the surface properties of fibers. Another option is polymer-based anti-static agents. These create a durable coating on textiles, offering long-lasting protection. Some products combine anti-static properties with other benefits, like softening or moisture control. This versatility makes them ideal for modern textile applications. Selecting the right type ensures optimal performance for your specific fabric and process.
Key Applications in Textile Processing
Anti-static agents play a vital role in various stages of textile production. During spinning and weaving, they prevent fibers from clinging together, ensuring smooth machine operation. In dyeing and finishing, these agents reduce static-related defects, improving the quality of the final product. Anti-static agents are also essential for synthetic fabrics like polyester and nylon, which are more prone to static buildup. By incorporating these agents, you can enhance efficiency, reduce waste, and produce textiles that meet high-quality standards.
Advancements in Anti-Static Agents by 2025
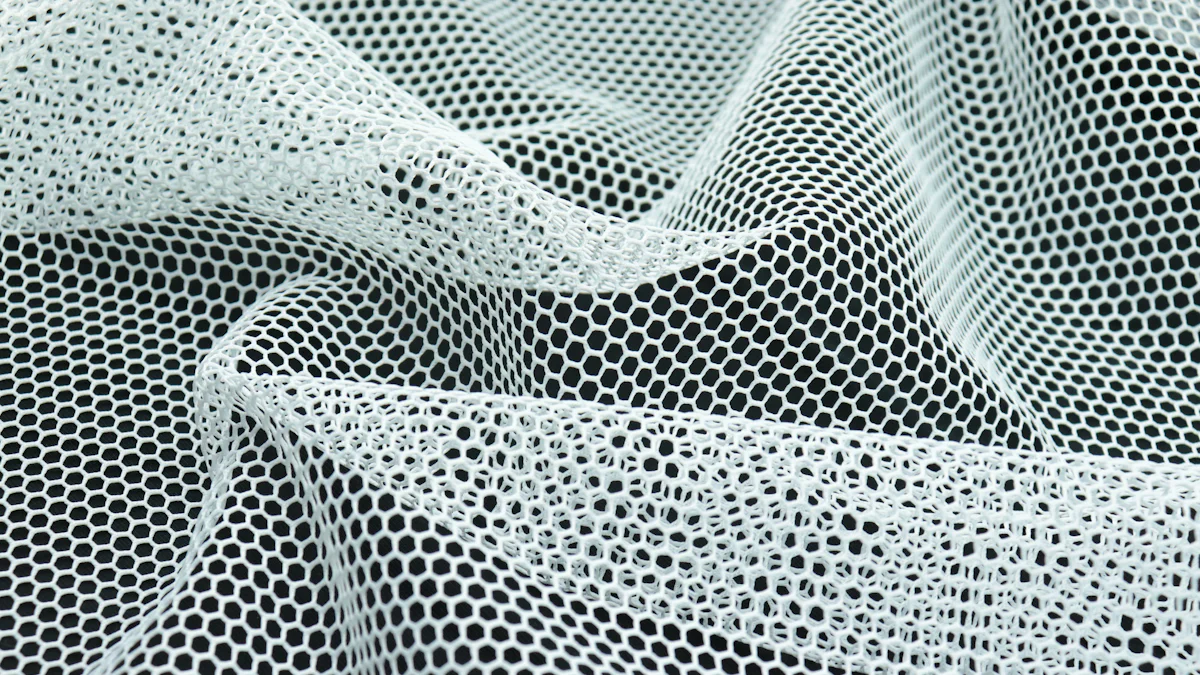
Innovative Materials and Formulations
By 2025, you can expect anti-static agents to feature cutting-edge materials and formulations. Manufacturers are now focusing on creating agents that work more efficiently across a wider range of fabrics. For example, polymer-based agents are becoming more advanced, offering longer-lasting static control. These formulations not only reduce static but also enhance fabric properties like softness and durability. Some products now combine anti-static functions with moisture control, making them ideal for synthetic fibers like polyester and nylon. This innovation ensures that your textiles maintain high performance throughout the production process.
Sustainable and Eco-Friendly Anti-Static Solutions
Sustainability is a growing priority in the textile industry. Anti-static agents are evolving to meet this demand. Many new formulations use biodegradable ingredients, reducing their environmental impact. You can now find agents free from harmful chemicals, ensuring safer use for workers and consumers. Some products even utilize plant-based materials, offering a natural alternative to traditional chemicals. These eco-friendly solutions align with global efforts to create greener manufacturing processes. By choosing sustainable options, you contribute to a healthier planet while maintaining efficient textile production.
Tip: Look for certifications like OEKO-TEX or GOTS when selecting eco-friendly anti-static agents. These labels ensure compliance with environmental and safety standards.
Integration with Smart Textiles and Advanced Manufacturing
The rise of smart textiles has created new opportunities for anti-static agents. These agents now integrate seamlessly with fabrics embedded with sensors or conductive fibers. This ensures that static electricity does not interfere with the functionality of smart textiles. Advanced manufacturing techniques, such as 3D knitting and automated weaving, also benefit from improved static control. Anti-static agents help maintain precision and efficiency in these processes. By adopting these innovations, you can stay ahead in the rapidly evolving textile industry.
Benefits of Anti-Static Agents in Textile Processing
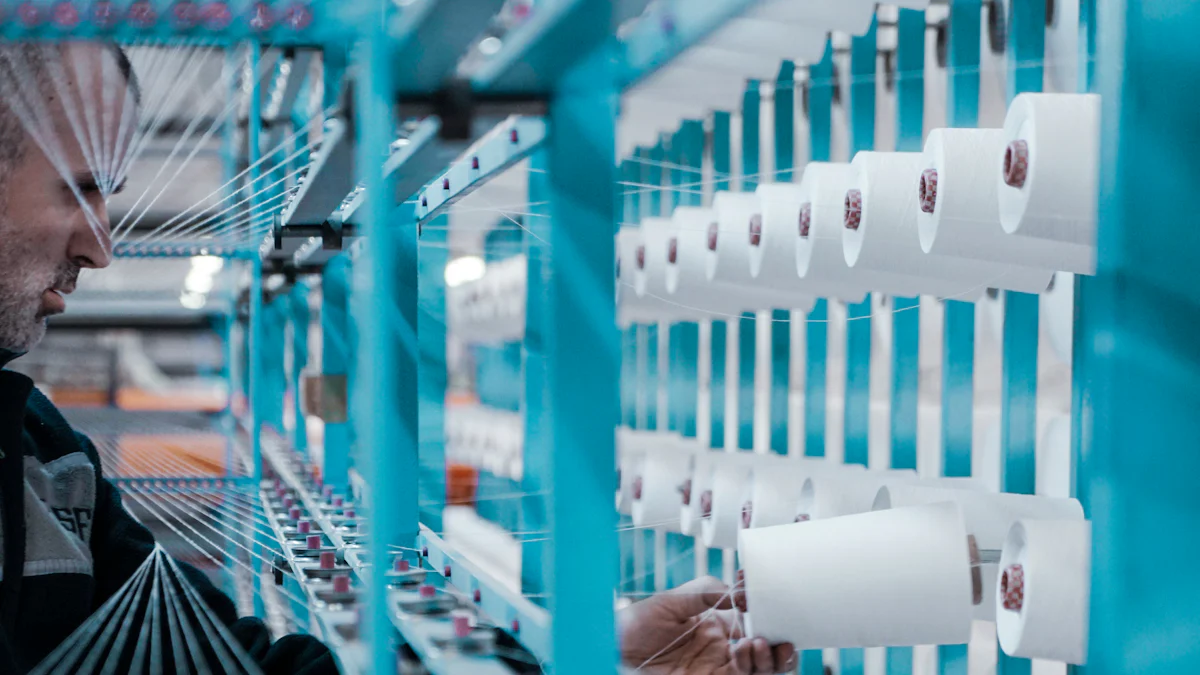
Enhanced Efficiency and Productivity
Anti-static agents improve the efficiency of your textile production process. Static electricity often causes fibers to stick together, slowing down machines and creating bottlenecks. By using these agents, you ensure that fibers move freely through equipment. This reduces downtime and increases the speed of production. You also experience fewer interruptions, which allows you to meet deadlines more consistently. Anti-static agents help you optimize machine performance, leading to higher productivity levels. With smoother operations, you can focus on scaling your production without worrying about static-related delays.
Improved Safety for Workers and Equipment
Static electricity poses safety risks in textile manufacturing. Sparks from static discharge can ignite flammable materials, creating hazardous conditions. Anti-static agents minimize this risk by preventing static buildup. This ensures a safer environment for your workers. Additionally, static electricity can damage sensitive machinery, leading to costly repairs. By applying anti-static agents, you protect your equipment from wear and tear caused by static. This extends the lifespan of your machines and reduces maintenance costs. A safer workplace and well-maintained equipment contribute to a more reliable production process.
Superior Quality and Durability of Finished Products
Static electricity can attract dust and dirt to your fabrics, lowering their quality. Anti-static agents prevent this by neutralizing static charges. This keeps your textiles clean and free from contaminants during production. These agents also ensure that fibers remain evenly distributed, resulting in smoother and more uniform fabrics. The final products not only look better but also feel more comfortable. Anti-static agents enhance the durability of your textiles, making them more resistant to wear and tear. This improves customer satisfaction and helps you maintain a competitive edge in the market.
Anti-static agents are transforming textile production by solving static electricity challenges. By 2025, these solutions will boost efficiency, sustainability, and innovation in the industry. Adopting them ensures you meet future demands while staying competitive. Embrace these advancements to enhance your processes and deliver superior textile products.
Post time: Jan-13-2025